Why Solar PV Panel Quality Matters – Even More Than You Think
Today I would like to talk about solar PV panel quality – and why it matters even more than you think.
If you’ve been looking into reducing your energy bills then solar PV is an awesome option, but there are a lot of different manufacturers out there and there’s a lot of claims around efficiency and who has the best panel. With this article I’d like to help explain a bit more about solar PV panels, what can go wrong with them, what questions you should ask and who in my opinion is the best investment and why.
You are potentially about to make a significant investment in a solar PV system for your home or business, and some people make the mistake, like I did when I first got into solar PV more than 13 years ago, that “A solar panel is a solar panel, what differences could there be between one manufacturer and another? We’ll just take what the supplier is offering and the cheaper the better.”
How wrong that opinion would turn out to be for me as I’ll explain further throughout this article.
It was when my wife and I were walking across a field carrying a Sharp solar panel to be installed and we realised how flimsy it was (the frame was bending in our hands), it kick-started a conversation that went along the lines of:
- “Crikey, this solar panel’s a bit flimsy? “
- “Do you think it’ll survive it’s warranty? “
- “I hope so, otherwise we’ll have a pretty annoyed customer and it’s fairly pointless installing something that’s going to landfill in the time period. “
- “Well, we’re building a business for the long-term, why don’t we find the best manufacturers with the best warranties and install them to an excellent standard so we’re really minimising the risk for our customers and the environment. “
And so began our journey into delivering outstanding solar installations using the world’s best kit.
Having offered maintenance & servicing callouts for years we’ve seen the great, the good, the bad and the ugly of solar PV. And the purpose of this post is to shine a light on Quality so that we can demand better of all manufacturers. Not only in our industry but also beyond so that it becomes standard practice for the environmental and social costs to be placed above the profiteering, exploitative and destructive business models that some manufacturers use.
So you’re thinking of investing in a solar PV system to reduce your energy bills, what you choose to put on your roof is the most important choice you will make as this is the most expensive area of the system to find and fix faults. Therefore minimising your risk for faults on the roof is what this is all about.
To give you a brief overview of where a solar panel can differ in quality at a very basic level, there are numerous key components to most solar PV panels:
Key Component Parts of a Solar Panel
- Glass
- Frame
- Laminate Backsheet
- Junction Box (with blocking diodes)
- Silicone Cells
- Intercell connections
Depending on the quality of manufacturing and materials will instantly affect what can go wrong with a solar PV panel.
What can go wrong?
- Potential Induced Degradation
- Light Induced Degradation
- “Snail-Trail” AKA Micro-cracks
- Laminate backsheet failure (allowing moisture in)
- Junction Box failure (allowing moisture in)
- Blocking diode failure
- Hot-spots
- Intercell Connection Failure
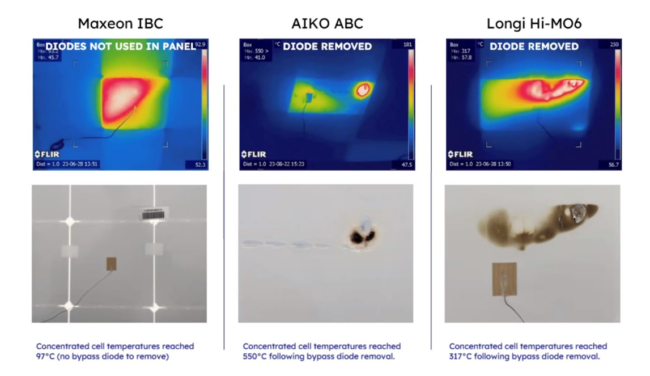
Image: Recent outdoor hotspot testing of Maxeon 6 AC vs. new competitor offerings
Without diving into the technical ins and outs of how and why each of these issues occur, the above issues will manifest as complete solar panel failure and therefore PV system shutdown or, possibly worse, significant degradation of performance that you may not pick up on for several years.
So the next step in this research into solar PV panels as an investment is to ask:
What happens if something goes wrong with a solar panel?
As I mentioned, when something goes wrong, your PV system will either stop generating or produce less power than it should. And unless a solar panel has caught fire (which is very rare, we’ve not seen a panel fire in 15 years so long may that continue!) or melted or cracked significantly, it won’t be obvious what the issue may be.
You should then call your installer (or us!) to investigate.
Your installer should try to diagnose the issue remotely first and then the next step is to visit site and carry out some tests. Normally there’s a callout fee (unless like with our own customers our callout fee is waived if your system is under our workmanship warranty and the manufacturer’s warranty).
Then, if the fault is on the roof (i.e. the solar PV panels) we then need to organise a roof inspection. This means access costs and labour costs.
Once we’re on the roof it can be a lottery as to how long it takes us to find the fault depending on what the fault may be.
If the solar PV panel laminate backsheet is bubbled and full of water, or if the Junction Boxes fall apart as we lift a solar panel, we can find this fault reasonably quickly and if the same issue is with 2 or 3 or more panels on the same array then we are safe to say that the solar panels are on their way out and need replaced.
However, less obvious may be PID where the voltage has essentially been sucked out of the solar panels gradually meaning the power output is at 80% or less of what it should be.
Even less obvious may be that the gradual degradation of the laminate backsheet and frame are allowing condensation in which causes the system to go into standby until the moisture evaporates.
Once we’ve identified the faulty solar panel(s) the next step is raising a warranty case with the manufacturer. And this can be a painful process.
The worst companies we’ve ever supported a customer through a warranty case were Canadian Solar and LG.
In the case of Canadian Solar we found 3 panels with identical intercell connection faults causing the laminate backsheet to melt and showing up as no system operation. This was a 3-year-old system and after 6 months of back and forth Canadian Solar agreed to ship 3 replacement panels to the customer but the customer would have to pay the 300 Euro shipping fee. And none of the solar PV engineers time (ours) nor the scaffolding costs were covered. The customer was concerned that more panels might fail and it took a further 6 months for Canadian Solar to agree to compensate the customer to replace all 28 of their panels.
Another case with LG was one where the string of LG panels after a few years was causing Low Insulation Resistance. LG wouldn’t accept our test results after the first callout and wanted us to attend site and test every single panel which we duly did proving that the insulation resistance on most of the panels was below what would allos the system to work. LG wouldn’t accept the results again and then proceeded to gradually ignore the customer until the customer decided to cut their losses and change their solar panels at their own expense.
And I know I’ve singled out Canadian Solar and LG here but over the years we have seen every single manufacturer on the market have a failure with their panels. Even the best manufacturers have failures.
As you’ve seen from these cases, having a fault on the roof is expensive. You have multiple visits to site, roof inspections, scaffold costs, admin time with reports and evidence to manufacturers. System down time. Stress. Money, unanticipated expenses. More stress.
So What Can I Do to Mitigate the Risk of Panel Failure:
- Research who is the best? That’s not as easy as you think as most manufacturer’s claim to be the best!
- Who stands by their product? Which warranty will cover labour and scaffold costs if their panel fails?
- Which manufacturers are ethical and responsible?
Of these 3 points, I know of only one solar panel manufacturer who offers a comprehensive warranty that covers labour and access costs and that SunPower – you can find out more about them here:
We have tested their warranty, yes one of their panels failed recently, and they were good to their word and reimbursed all of costs with no cost to the customer. Happy days.
They also have Cradle2Cradle certification and are a market leader in their manufacturing processes and supply chain to minimise their environmental impact and ensure there’s not a high environmental or social cost to their product.